Formfleece
We are one of the leading specialists for molded parts made of nonwoven fabrics. Formfleece always consists of a base fiber and a matrix fiber for shaping. The matrix fiber has a different melting behavior and melts at lower temperatures. This means that a sheet of fleece can be thermoplastically formed by heat and cooling. A special property of the molded fleece is its sound-absorbing effect; molded parts made of fleece therefore have a positive effect on room acoustics. At the same time, the molded parts are impact-resistant, have a pleasant feel and a special look.
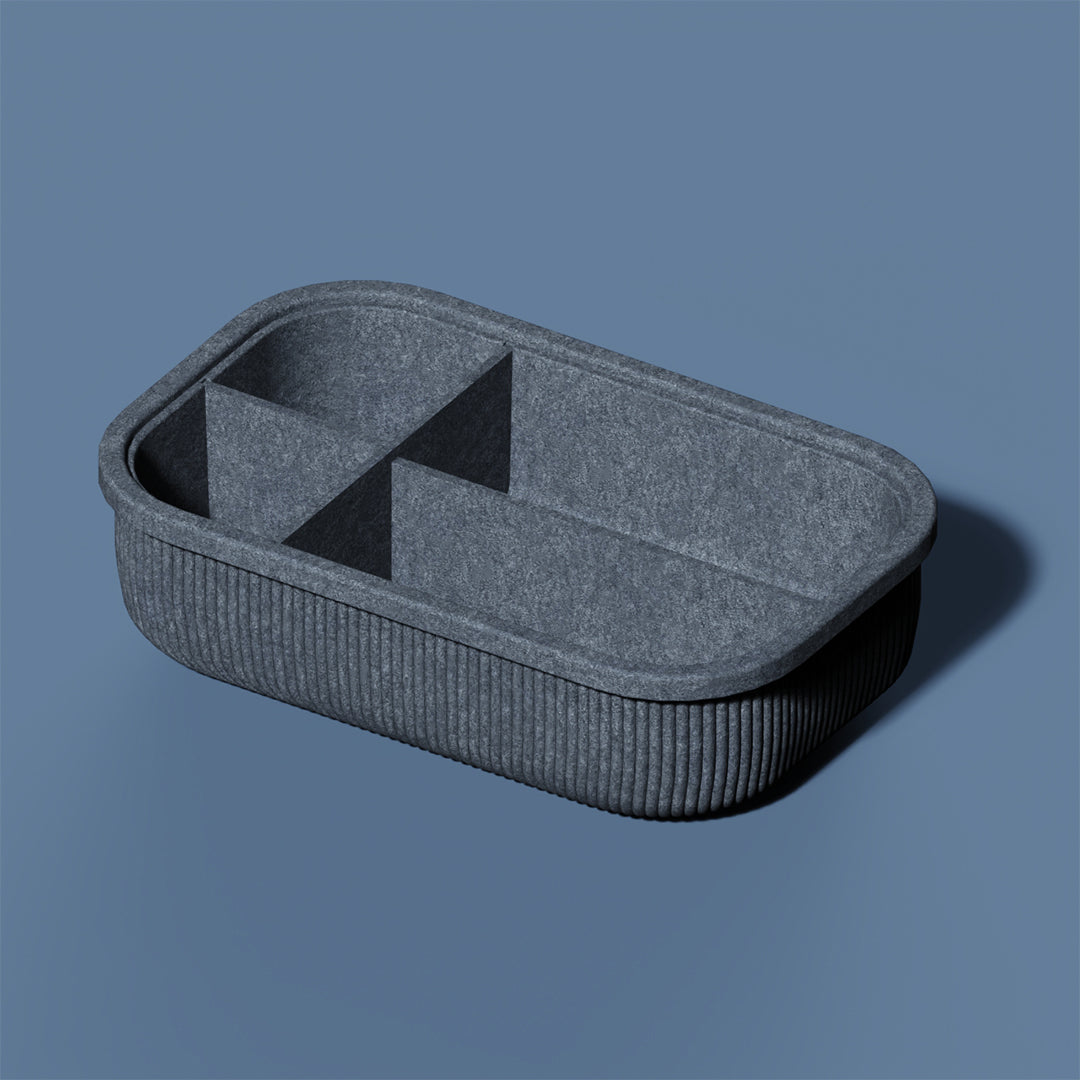
Formshaped Fleece Parts
Fleece materials can be transformed into 3D molded parts by compression molding. Molded fleece has similar stiffness and strength to a conventional plastic molded part, but does not lose its nonwoven structure and felt-like surface. Molded parts made of fleece materials are therefore very suitable for applications in the technical or acoustic sector. The production of nonwovens makes it possible to use materials from recycled or renewable sources, so that products made from them are sustainable.
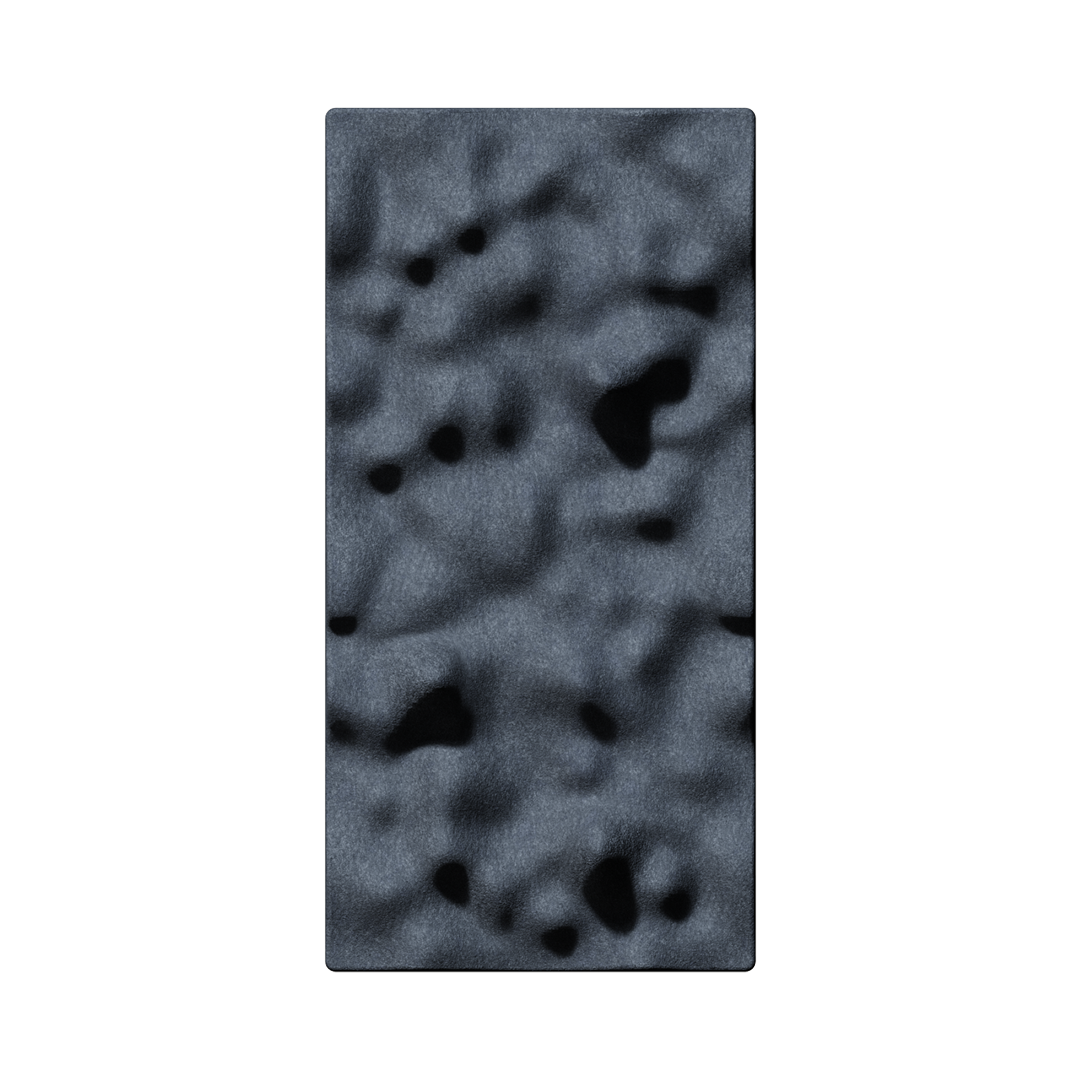
Up to 100% Recycling Origin
Polyester Formfleece
Polyester formfleece is a nonwoven consisting of polyester mono-material with a specific
proportion of polyester bicomponent fibers for thermoplastic processing. Due to its versatility and durability, polyester formfleece is a preferred material in numerous industries. It is lightweight, resilient, and insulating. In addition to its mechanical properties, it offers a significant design advantage. The material can be dyed in any conceivable color, has an attractive texture, and simply looks appealing. Furthermore, the raw material can be blended with darker fibers to achieve a mottled appearance.
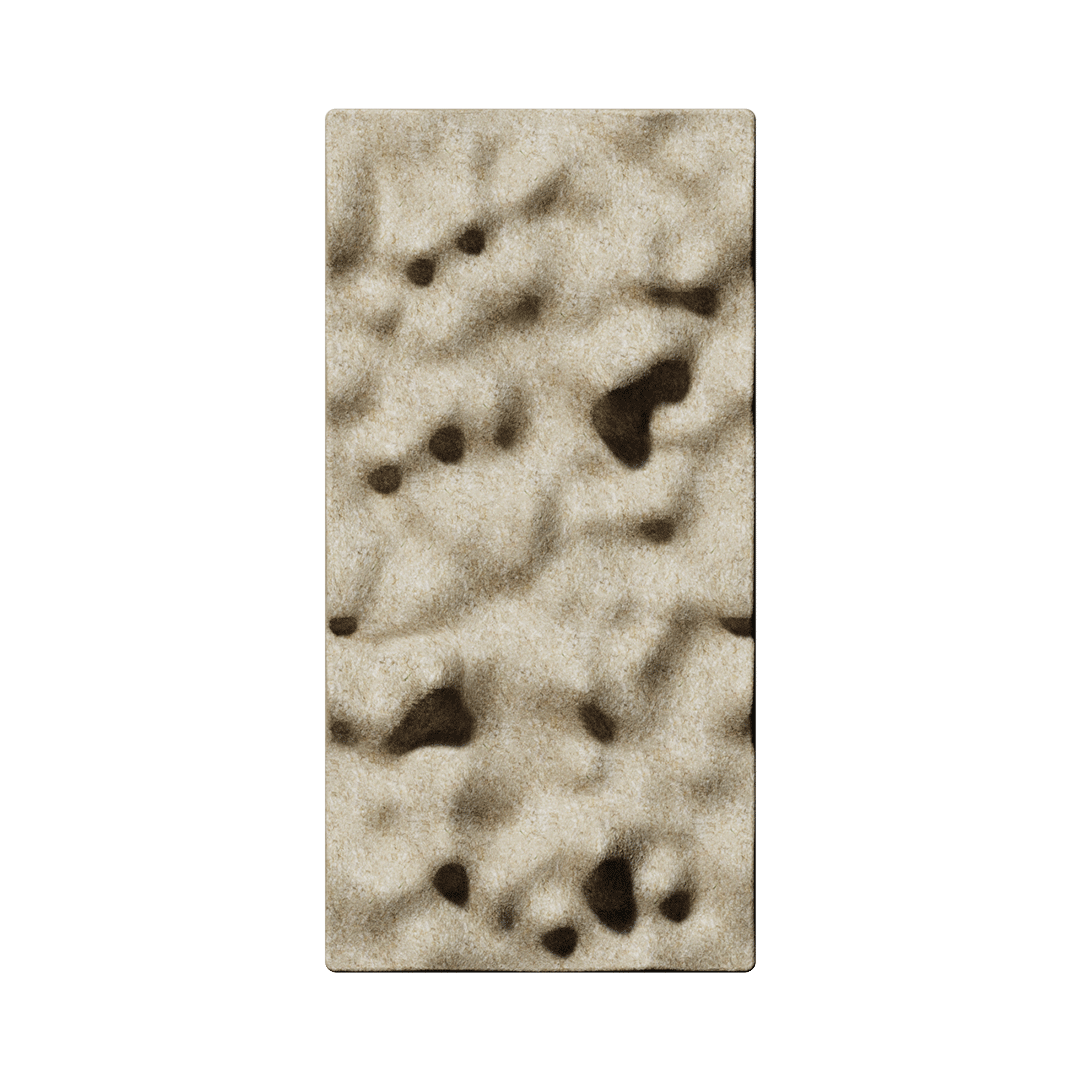
Biobased and degradable
Natural Fiber Formfleece
Natural fiber formfleece is made from natural fibers such as hemp and flax, combined with a matrix that provides strength, allowing them to be thermoplastically processed. These nonwovens are lightweight yet comparatively stiff and strong, making them functionally competitive with non-bio-based nonwoven materials. They are light, insulating, and elastic. The cultivation of fast-growing natural fibers is sustainable and has no negative impact on the soil. This makes them a genuine alternative to petroleum-based materials. When combined with a biodegradable matrix fiber, the nonwovens are even naturally biodegradable.
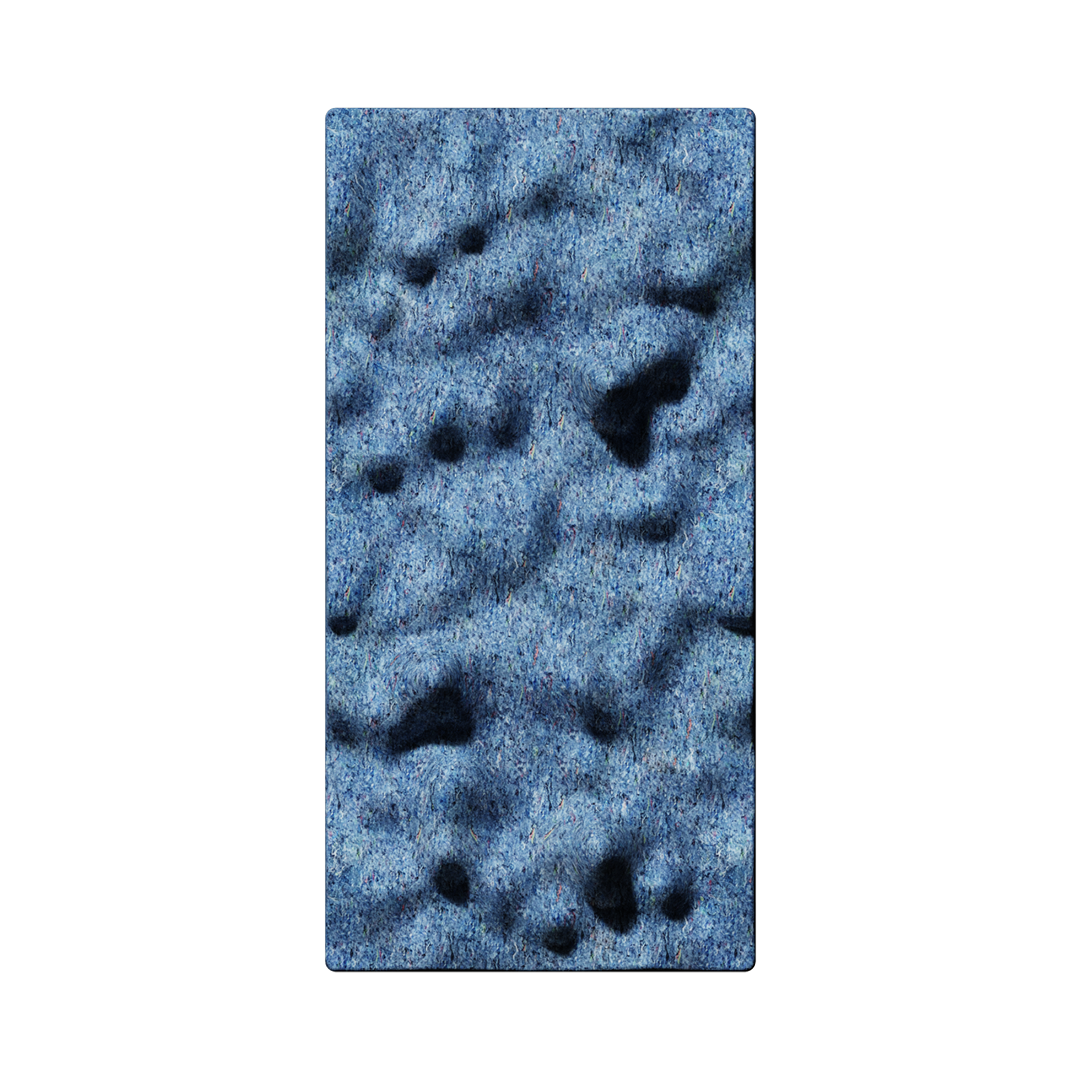
Made from Textile Waste
Upcycling Formfleece
Upcycled fleece is made from recycled clothing and textiles. As a result, the nonwoven often contains a variety of different textiles, making various colors visible on its surface, which gives it a unique appearance. Upcycled nonwovens behave similarly to other types of nonwovens, offering insulation, stability, and durability. They are lightweight yet comparatively stiff and strong. Since only recycled materials are used in production and nothing new is manufactured, they represent an environmentally friendly alternative. The mechanical recycling process requires little energy and allows textiles, which often have no further use, to be repurposed in a meaningful way.
Selected Projects
-
Neverfeltsogreat | Mag Rack
Home organisation
-
Reiss Büromöbel | Uni
Acoustic partition system
-
Orangebox | Coppice
Acoustic partition system
-
Neverfeltsogreat | A4 Tray
Office organisation
-
Herman Miller | Kivo
Acoustic partition system
-
Neverfeltsogreat | Divider
Acoustic partition system
-
Cabs Design | Quadrum
Acoustic wall system
-
Headsprung | Flutter
Acoustic wall system
-
VS Spezialmöbel | eddy
Carrying bag for flexible working
-
Cabs Design | Wing
Acoustic ceiling system
-
Neverfeltsogreat | Boxes
Office organisation
-
Hibudie | Box
Storage
Functional and Design Solutions
Press Lamination
When pressing fleeces, we can press an outer layer onto the fleece material in the same step. This is done without additional passes or adhesives. The reasons for this can be both optical and functional: For example, a film can be applied to make the molded part less sensitive to moisture, or an individual print can be used for special designs.
Attachments and Finishing
After the shaped part has been pressed and, if necessary, cut to size, our work is not yet done. Depending on the wishes and requirements of our customers, we offer the application of various additives to complete the product. Unconventional applications are also possible - our team will find the right solution.
Recycling of Fleece Products
-
Monomaterials
There are various recycling options for monomaterials such as polyester fleece. End products and production waste can be mechanically shredded and incorporated into a new fleece. This requires very little energy. The recycling waste replaces part of the new material. Alternatively, the waste can also be thermally processed into new fibres. This ensures that the fibres from the same product are used again and again for the product. Both open-loop and closed-loop recycling options are possible.
-
Composite Materials
Composite materials can be mechanically shredded and incorporated into a new fleece material. This requires very little energy. The recycled waste replaces part of the new nonwoven. This ensures that the fibres from the same product are used again and again for the product. We can therefore ensure that there is a closed-loop recycling option for composite materials at the end of the product life cycle.