Knife Cutting
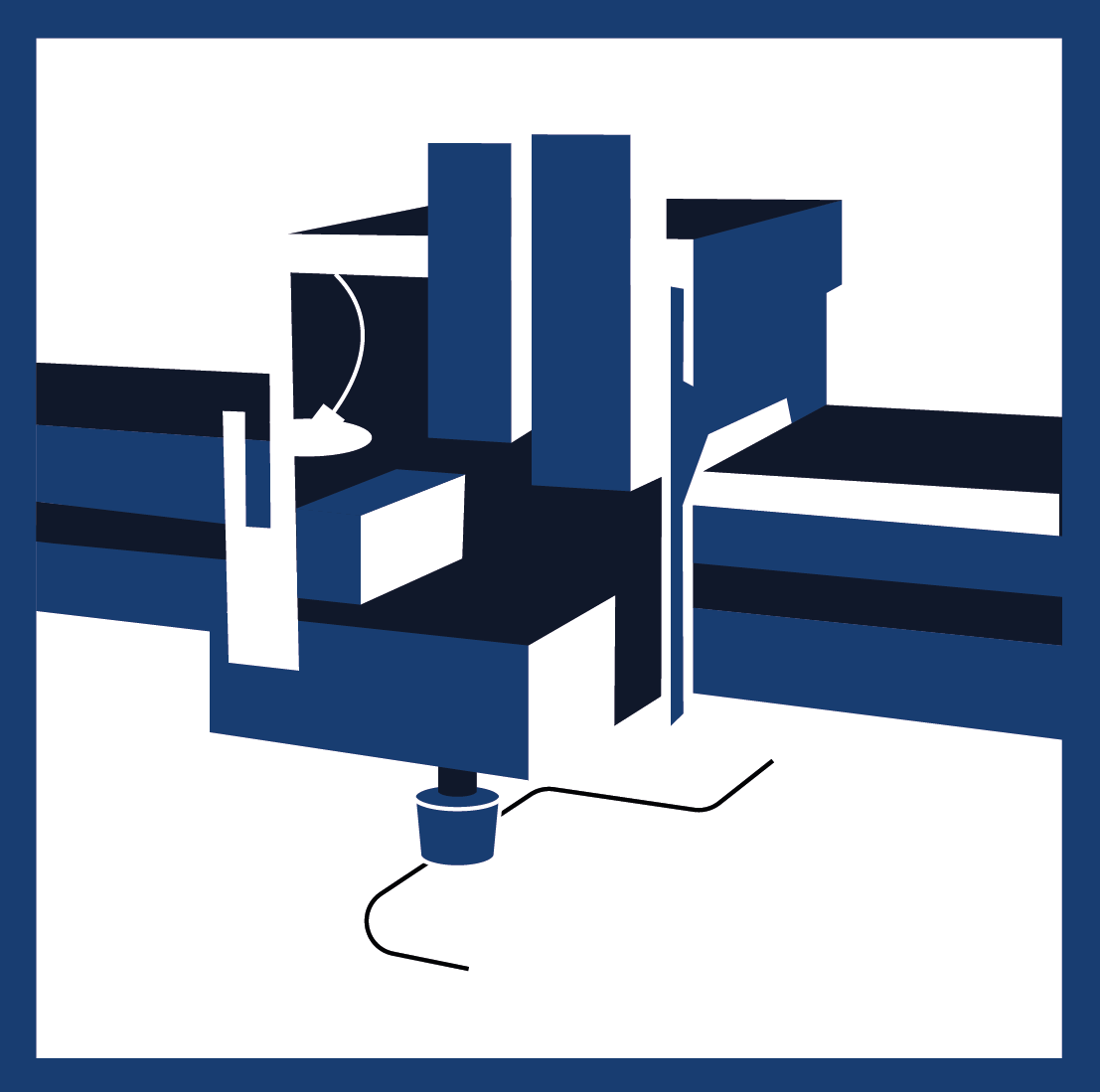
Exciting Advantages of CNC-Knife Cutters
-
Cutting Patterns Are The Core of Knife Cutting
Cutting patterns are crucial for textile cutting machines as they enable the precise and efficient processing of fabrics. They serve as a digital template that informs the machine which areas of the material should be cut. A well-optimized cutting pattern ensures that the machines work with high accuracy and minimizes material waste. It also enables faster production and higher quality end products, as errors and inaccuracies are avoided. Cutting patterns therefore not only help to increase efficiency, but also to reduce production costs.
-
We Continuously Optimize Fabric Cuts
Efficient fabric cutting planning is crucial for optimizing production. Precise cutting can reduce material waste and costs, resulting in better use of resources. In addition, well thought-out cutting helps to increase production speed and minimize the amount of work involved. Minimizing waste not only reduces material consumption, but also reduces the environmental impact. This is why we continuously optimize and review our cuts.
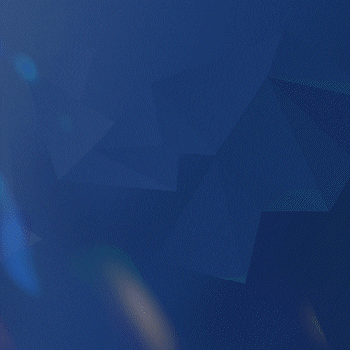
Technical Details
Working Size
Up to 2000 mm width, endless length