Milling
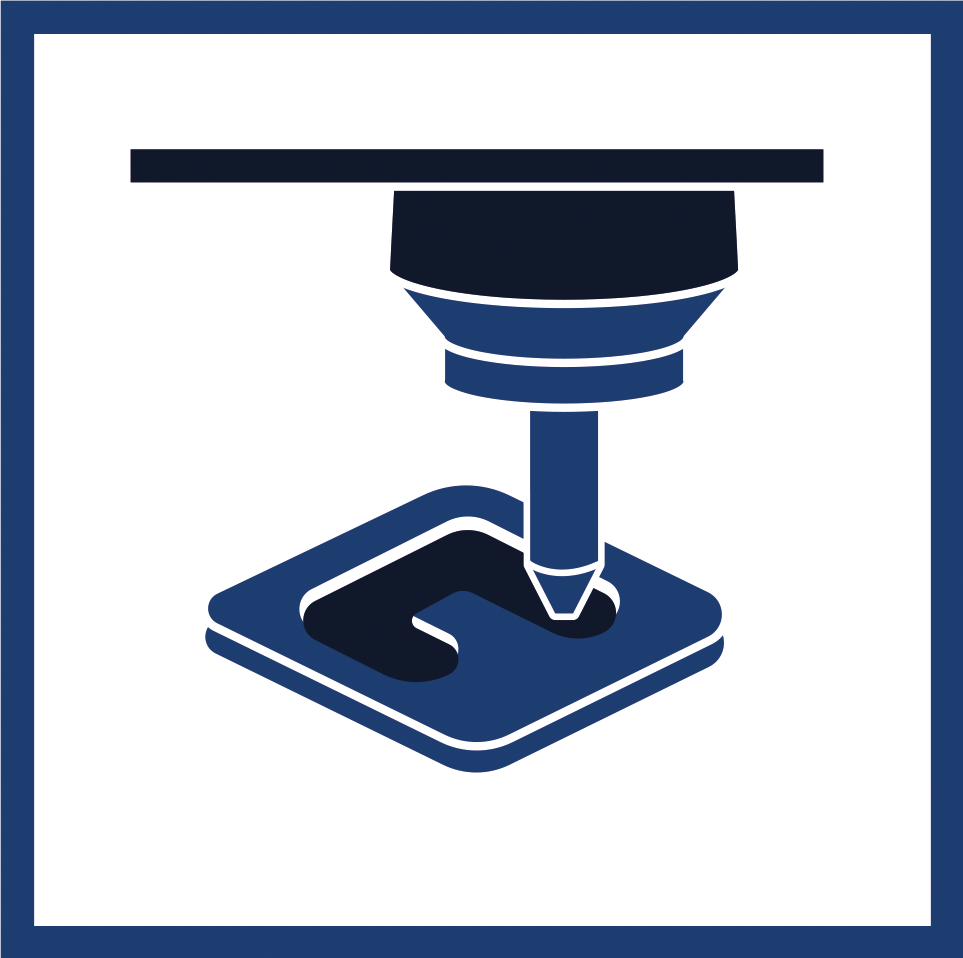
Special Properties of Plastic, Fleece and Wood
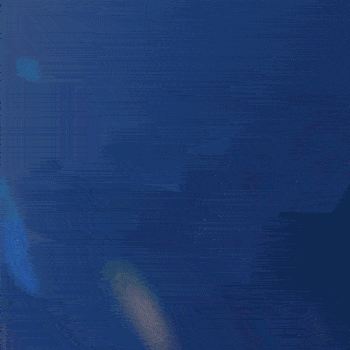
Technical Details
Working Size
4-Axis Milling: 2050 x 3050 x 270 mm
5-Axis Milling: 2205 x 3100 x 378 mm
Optimizing Milling
The basis for the best milling results is to fix the part or the board to be milled, for example using a multi-zone vacuum table. This way we can create warp-free workpieces. A milling head used for plastic is very sharp and moves extremely quickly. There are special spindles specially designed for plastics. Consistent cooling of tools and workpieces via minimum lubrication or spray cooling is necessary for plastic milling, since these can melt even at low temperatures. This requires a precise adaptation of the milling head to the material. Since plastics are very different, it is often necessary to test here to find the optimal combination of moving speed and rotation.