Thermoforming
Thermoforming of Plastics
Pressing Thermoplastics Into Shape Using Heat and Vacuum
In thermoforming, a plastic sheet is heated to transform the material from a rigid to a malleable state. A vacuum is used to thermoform the plastic using a tool and shape it into the desired form. To ensure that the part ultimately retains its shape, it is then cooled to a certain temperature by a blower. After this step, the raw part is almost finished. After the processed piece has been “demolded”, i.e. removed from the tool, and the excess material has been trimmed at the edges, the part is ready for further machining in our in-house production.
How the Thermoforming Process Works
Thermoforming is particularly suitable for the fast and cost-effective production of medium to large quantities of parts: The process is characterized by large purchasing volumes of starting materials, low tooling costs and fast process times. The length of the throughput time depends on the material and mold, but is in any case only a few minutes. This means that a considerable number of items can be produced in a short time.
At the same time, there are many aspects that can be determined individually for each project. The selection of plastics that we can process is very broad - the material can be selected depending on the focus of the project, particularly for purposes such as weather resistance and impact resistance or also for particular freedom when designing products. Material combinations can also be created, for example in the form of a base layer of cost-effective ABS and design laminations.
How Thermoforming Works – Explained Compactly in Video
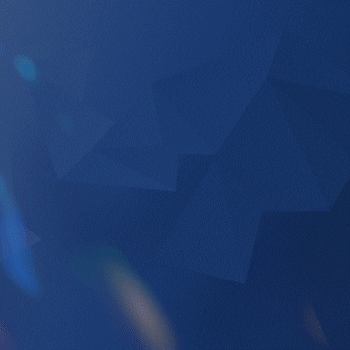
Technical Details of Our Production
Types of Machine for Plate Materials
Automated plate thermoforming machine
Work Surface of Our Thermoforming Machine
Up to 1500 x 1000 x 600 mm
Plastic Materials We Process
We process plastics of all kinds. We use thermoforming to create drawn parts from thermoplastics such as ABS, polypropylene or polycarbonate as well as material mixes with PMMA, ASA or TPU. With our process-controlled sheet forming machine, we achieve an efficient cycle rate and consistent product quality. The special feature of thermoplastics is that they can be melted and reused several times.
Areas of Application for Thermoformed Parts
Thermoformed products are suitable for many areas of application. For our own brands, we use this process to produce trays and cases that are particularly resistant to weathering and heat. Protection against electricity and UV rays is also a special property of the material, which can be essential for certain molded parts.
Preprogrammed Accuracy of Plastic Molded Parts
In the thermoforming process, we can precisely calibrate the various process steps such as duration, heating phases and cooling. Once the perfect settings have been found, our machine saves these for usage in later projects. This way we achieve a high and consistent quality level, even across large commisions and long partnerships.
Frequently Asked Questions About Thermoforming
Molds & Tools
Tools are made specifically for each molded part and are milled from aluminum. We use wood or ureol for prototypes.
Quantities
The thermoforming process is suitable for medium to large series. It usually pays for itself from approx. 1,000 parts over the running time.
Temperatures
Depending on the material, it is heated to approx. 130°-220°. This ultimately depends on the material and is determined by the thickness, texture and desired properties of the final part.
Development time
It generally takes 4 to 6 weeks after the drawings for the desired part are ready to create a prototype.A series tool takes between 8-10 weeks, so that the first series production can usually start after 8 weeks.
Stability
Thermoplastics harden to form very stable molded parts.They are difficult to bend, cannot be deformed when cold and are scratch-resistant.
Materials
We process a wide variety of thermoplastics with individual properties and characteristics.The right material is selected for each project.
Recycling
Plastic waste and old thermoplastic products can be granulated several times and reprocessed into sheet products.