Waterjet Cutting
Precision Cutting at High Pressure
Waterjet cutting is a cold cutting process with minimal material loss. The cut is not created by heat or the use of a knife, but only by water, which cuts the material at high pressure. The workpiece is processed with the water jet without the cutting edge being ground out. The thinner the material thickness, the clearer the results. The process allows several work steps to be combined in a time-saving manner and achieves an exceptional cutting performance. We can therefore also produce very complex shapes with precision and clean cut edges. To do this, we use waterjet machines, which can be moved in 3D space in specific. The waterjet is equally suitable for small and large series, as cutting patterns can be created with relatively little effort and the cutting process is very fast.
Pure Waterjet Cutting
We only use environmentally friendly pure water cutting. This means that no abrasive substances are added to the water used to facilitate cutting. The water is therefore used in its pure form without any additives. This process is particularly suitable for slightly softer materials such as those we primarily work with: Textiles, thermoplastics and nonwovens. With pure water cutting, the jet has a very small diameter and can therefore cut very precisely. Waterjet cutting is also very environmentally friendly. No gases, water pollution, chips, dust or air pollution are produced. We use the water used as a recycled material.
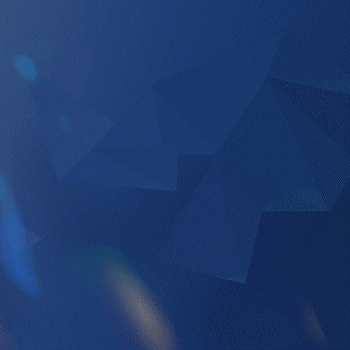
Technical Details
Size 3D
2200 x 1200 x 700 mm
Size 2D
2000 x 1000 mm
Clear Advantages of Waterjet Cutting
The waterjet has convincing advantages over other cutting methods. It achieves a cold and gentle cut with extremely high precision. In addition, the material is not altered, distorted or damaged during the cutting process. The use of waterjet technology means that there is little or no need for post-processing of the molded part, as the cuts can be made with high precision and achieve a high level of quality.
We use the waterjet to cut plastics, textiles, elastomers, thermoplastics, fibrous materials or even foams and insulating materials. The process is particularly important when cutting composite materials, for which the waterjet is perfectly suited. We often use waterjet cutting directly for the further processing of molded parts that we have processed ourselves with our molding presses in a previous step. This allows us to combine several production steps in a short space of time and deliver a finished part to our customers without having to rely on external service providers.
Materials We Process
We specialize in cutting softer materials. These include plastics and fleece materials, and we also process composite materials such as natural fiber-reinforced plastics, foams and rubber.
How Waterjet Cutting Works
Precise Coordination and Programming
Every project and every material is individual and we also map this process with us. To do this, we combine CAM-controlled programming with test trials in order to realise the optimal processing.